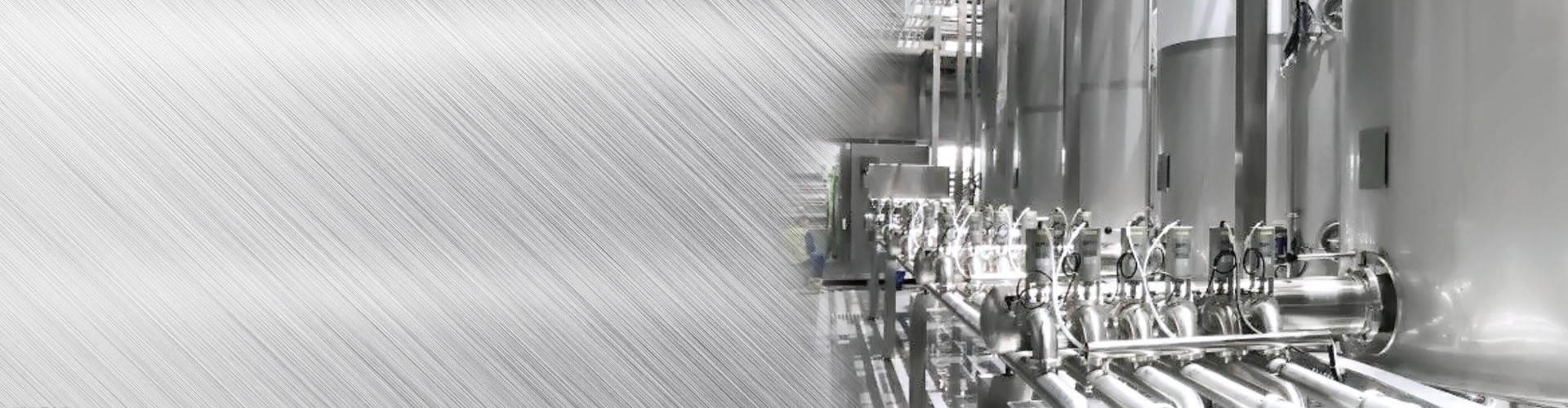
Pasteurization is a process named after the scientist Louis Pasteur. It kills pathogens in food by heating. For the dairy industry, the terms "pasteurization", "pasteurization" and similar terms refer to the process of heating each particle of milk or milk products to one of the temperatures given in the following table in properly designed and operated equipment and continuing at or above that temperature for at least the corresponding specified time:
63 º C (145 º F) * 30min vacuum pasteurization
72 º C (161 º F) * 15s high temperature short time pasteurization (HTST)
89 º C (191 º F) 1.0 s HHST
90 º C (194 º F) 0.5 second HHST
94 º C (201 º F) 0.1 s HHST
96 º C (204 º F) 0.05 seconds HHST
100 º C (212 º F) 0.01 seconds HHST
138 º C (280 º F) 2.0 seconds ultra pasteurization (UP)
Temperature time pasteurization type
69 º C (155 º F) 30 min vacuum pasteurization80 º C (175 º F) 25 seconds high temperature short time pasteurization (HTST)
83 º C (180 º F) 15 seconds high temperature short time pasteurization (HTST)
The original pasteurization was barrel pasteurization, where milk or other liquid ingredients were heated in a large pot for at least 30 minutes. It is now mainly used in the dairy industry to prepare starter cultures in cheese, yogurt and buttermilk, and to pasteurize some ice cream mixtures.
Today, the most common pasteurization method in the United States is high-temperature short-time (HTST) pasteurization, which uses metal plates and hot water to raise the temperature of milk to at least 161 ° F for at least 15 seconds, and then quickly cools. High temperature short time (HHST) is a process similar to HTST pasteurization, but it uses slightly different equipment, with higher temperature and shorter time. For products considered to be ultra pasteurized (UP), they must be heated to no less than 280 ° for two seconds. The UP pasteurization can make the product have a longer shelf life, but it still needs to be refrigerated.