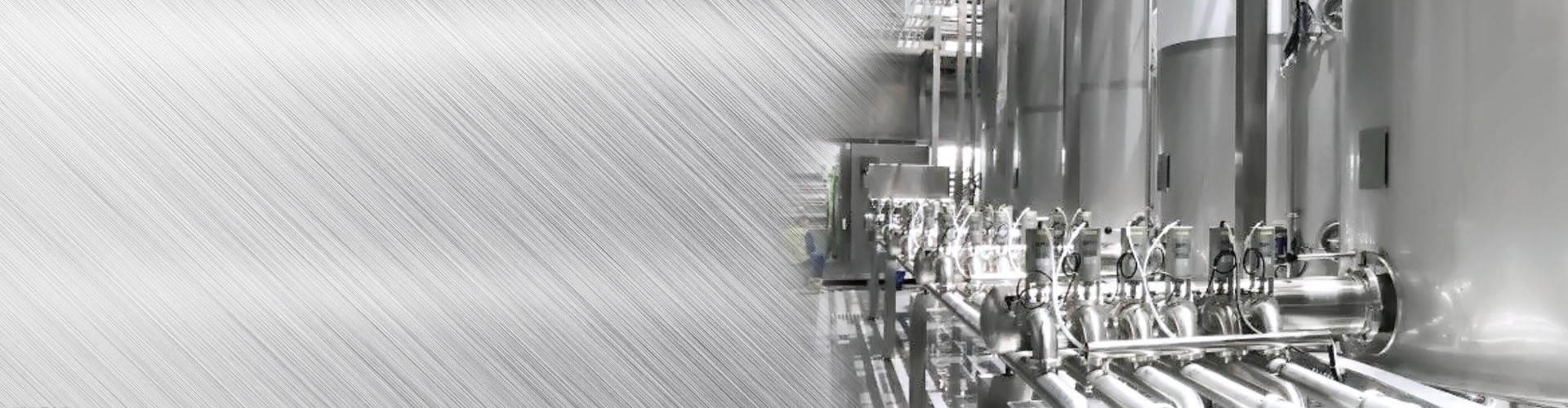
Los productos lácteos son medios naturales de cultivo para microorganismos y son vulnerables a la corrupción y el deterioro en el medio ambiente debido a múltiples factores. Desde la leche cruda hasta el producto terminado, los productos lácteos han experimentado tuberías y equipos como pretratamiento, ingredientes, homogeneización, esterilización, llenado y embalaje. con la profundización de la automatización, diversificación y alta gama de los equipos lácteos, si se produce una avería, los operadores de primera línea y los trabajadores de mantenimiento deben resolver rápidamente la avería manteniendo la limpieza del equipo para Garantizar la puntualidad y la seguridad. Por lo tanto, este artículo propone el concepto de mantenimiento de producción total (tpm) y aplica el pensamiento TPM a la gestión de equipos lácteos, con el objetivo de mejorar la capacidad de todo el personal para analizar, tratar y resolver fallas, aumentar la conciencia de mantenimiento previo de los trabajadores de mantenimiento, aumentar el entusiasmo y la participación de todo el personal, fortalecer La comunicación y escoltar productos de alta calidad.
El tpm, es decir, la participación total en el mantenimiento de la producción, es propuesto e implementado por la Asociación Japonesa de gestión de equipos industriales, para optimizar el rendimiento del equipo mediante el establecimiento de un sistema en el que participen todos los empleados y se centren las actividades de mantenimiento de la producción, transformando el mantenimiento posterior en mejorar el mantenimiento y El mantenimiento de la producción. El TPM tiene tres características: eficiencia total, participación de todo el sistema y todo el personal. El objetivo de la teoría del TPM es establecer y mejorar un sistema empresarial que limite la eficiencia del sistema de producción de autoayuda. desde el conjunto del sistema de producción, todos los departamentos funcionales, incluida la producción, el equipo y la gestión, construyen un mecanismo que pueda "prevenir problemas antes de que ocurran". a través de la participación de todo el personal desde El nivel superior de la empresa hasta los empleados de primera línea y las actividades continuas de mejora de pequeños grupos, finalmente se alcanzan los objetivos de cero accidentes, cero malas condiciones, cero pérdidas, cero fallas y cero paradas cortas.
2.1 estructura de la dirección del TPM
Para adaptarse a las necesidades de desarrollo de la producción, fortalecer la gestión y el mantenimiento de los equipos y garantizar la puntualidad, pertinencia y eficacia del mantenimiento de los equipos, es necesario establecer una estructura de responsabilidad de trabajo TPM de primera línea, una estructura de gestión de tres niveles de Jefe de equipo, Jefe de equipo regional y Jefe de equipo, es decir, operador, para autorizar plenamente la División del trabajo y hacer que el trabajo sea más específico, consciente y autónomo. Los responsables de todos los niveles del TPM y el calendario de mantenimiento mensual se muestran en la figura 1.
El Jefe general del equipo coordina los objetivos de la gestión del TPM y supervisa el funcionamiento diario del sistema. es necesario tener una comprensión integral y general del ciclo de programación del equipo y el Estado del equipo. la responsabilidad principal es comprobar el mantenimiento de todo tipo de fallas del equipo, mantener una buena comunicación con el supervisor de mantenimiento o el reparador y mejorar la capacidad de análisis y resolución de las causas de fallas. Proporcionar apoyo y ayuda al trabajo del Jefe del equipo regional, como la intervención oportuna para hacer un seguimiento de sus problemas pendientes; Monitorear la implementación de proyectos de mantenimiento trimestrales, como varios tipos de filtros de aire de equipos, varios filtros de agua, lámparas bactericidas ultravioleta, anillos de Goma de válvulas, accesorios vulnerables, etc.
El Jefe del equipo regional es el Jefe que es bueno en el funcionamiento y mantenimiento de un determinado tipo de equipo, y es la figura central que desempeña un papel clave directo en la promoción general del tpm. La responsabilidad principal es ayudar activamente a mejorar la capacidad operativa de los operadores a cargo de cada equipo, enseñar a compartir la experiencia del equipo y la capacidad de manejar y resolver fallas simples; Comprobar si el trabajo diario de mantenimiento de cada operador está en su lugar y organizar la implementación o ajuste del plan de mantenimiento a tiempo; Tomar la iniciativa de implementar el trabajo de mantenimiento semanal y revisar cuidadosamente los registros de mantenimiento; Participar en el trabajo de mantenimiento mensual de ayudar a los trabajadores de mantenimiento y revisar oportunamente los registros de mantenimiento anuales y mensuales.
2.2 elaborar un formulario de registro de trabajo diario
Elaborar un formulario de trabajo del sistema tpm, que incluye un formulario de registro de mantenimiento para registrar los artículos de falla y la duración de la falla, registrar la participación del personal de mantenimiento del equipo en el formulario de registro de mantenimiento temporal, registrar el mantenimiento diario convencional no temporal, el mantenimiento semanal, el formulario de registro de mantenimiento anual, registrar el Formulario de registro de reemplazo de piezas vulnerables y el formulario de registro de mantenimiento de varias herramientas (carretillas elevadoras, limpiadoras, máquinas de pulverización), etc. Después de la formulación del formulario tpm, es necesario capacitar e implementar a los operadores para rellenarlo cuidadosamente, y el jefe regional del equipo y el Jefe general del equipo lo confirman regularmente para formar el mecanismo diario de operación y supervisión del sistema tpm. La tabla de registro de fallas de mantenimiento se muestra en la figura 2.
2.3 Formar un informe de análisis mensual del Estado de funcionamiento del equipo
El objetivo final de las estadísticas de fallas es formar un informe general de análisis del Estado de funcionamiento del equipo a través del análisis integral de los datos. Cada mes, es necesario ordenar el tiempo de falla, el tiempo de funcionamiento, el tipo de falla y los cambios interanuales en la tasa de falla de cada máquina, comparar los datos de funcionamiento del equipo, reflexionar sobre la tendencia de falla del equipo, analizar específicamente las causas de falla de varios equipos y hacer predicciones de puntos de falla de riesgo, hacer sugerencias de mejora y establecer objetivos de mantenimiento para la próxima etapa del equipo. El informe mensual de análisis del equipo finalmente debe presentarse al Departamento de gestión del equipo, y el personal relacionado con el equipo debe aclarar las prioridades y direcciones de trabajo para el próximo mes.
El informe de análisis mensual no solo puede servir de referencia y guía para establecer medidas de mantenimiento, sino que también puede proporcionar soluciones e inspiración para futuras máquinas de mantenimiento. Cuando se produce una falla, los operadores y los trabajadores de mantenimiento a menudo tardan mucho tiempo en juzgar la falla, y hoy en día, rastreando los registros de falla anteriores del mismo equipo, en comparación con las características de falla anteriores verticalmente, se puede determinar el quid de la falla y las contramedidas más rápidamente.
2.4 Promover el proceso de mantenimiento
2.4.1 Identificación de los puntos de mantenimiento de la gestión
A través de la consulta, visita e inspección, se adquieren gradualmente todos los puntos de mantenimiento del equipo y se añaden señales para posicionarse junto a las partes de mantenimiento, que recuerdan visualmente a los operadores el mantenimiento diario. Al utilizar palabras e imágenes simples para presentar los requisitos específicos de mantenimiento, los operadores tienen una comprensión clara de la ubicación, frecuencia, métodos de mantenimiento y requisitos de cumplimiento del mantenimiento preventivo del equipo, y los operadores solo necesitan hacer un buen trabajo de mantenimiento del equipo de acuerdo con las regulaciones estándar.
2.4.2 implementación de la inspección puntual antes del turno y el mantenimiento después del turno
Antes de arrancar el equipo, el operador debe hacer una evaluación general del Estado general del equipo. La simple inspección puntual no solo permite a los operadores tener una buena idea de la situación del equipo, sino que también evita accidentes accidentales. Si las herramientas de mantenimiento restantes están en el mecanismo de transporte en el lugar, una vez que el equipo funciona, puede causar accidentes de impacto graves; Las válvulas de agua, electricidad y gas del equipo no encienden el interruptor antes de que el equipo comience, y todas las agujas indicadoras del monitor no están dentro del rango adecuado, lo que puede causar daños en los accesorios debido a la acción descoordinada del equipo, lo que resulta en trabajos de mantenimiento adicionales.
El mantenimiento después del Trabajo también es igualmente importante, con el objetivo de garantizar que las piezas vulnerables y las partes vulnerables del equipo estén lubricadas en su lugar y se mantengan en las mejores condiciones. Después del mantenimiento, el operador debe registrarse en la columna correspondiente del formulario de mantenimiento y debe firmar y confirmar el Jefe del equipo regional.
2.4.3 implementación del mantenimiento mensual y el mantenimiento anual
El Jefe general del equipo debe determinar el tiempo de mantenimiento mensual con el personal de gestión de mantenimiento y llegar a un consenso sobre el mantenimiento de todo el personal. El mantenimiento mensual regular se realiza de acuerdo con el tiempo prescrito. Además, el mantenimiento anual se lleva a cabo durante la temporada baja de producción. En el trabajo real, los puntos de mantenimiento y los programas de limpieza deben actualizarse regularmente. a medida que el trabajo de mantenimiento se lleva a cabo en profundidad, algunos puntos de mantenimiento ignorados serán excavados gradualmente por operadores o reparadores, mientras que algunos puntos de mantenimiento no esenciales deben cambiar la frecuencia de verificación del efecto de mantenimiento. los puntos de mantenimiento dinámicos pueden mantener el trabajo de mantenimiento optimizado y eficiente.
Para las empresas lácteas, el invierno es la temporada baja. Es una práctica más científica utilizar la temporada baja para el mantenimiento anual y aprovechar al máximo el tiempo libre para ajustar el Estado del equipo.
Por un lado, el mantenimiento anual sanitario del equipo, que solo necesita ser llevado a cabo por el operador, debido al funcionamiento perenne del equipo, debe esconder suciedad en algunas partes ocultas, en este momento, la limpieza profunda puede renovar el entorno sanitario del equipo. Antes de la limpieza, se debe identificar el punto ciego sanitario y formular un plan de mantenimiento sanitario específico de acuerdo con los resultados de la identificación, que incluye el equipo objetivo, la parte o el contenido de la limpieza, el personal de mantenimiento, la fecha prevista, la fecha de finalización, el personal de aceptación, los problemas existentes y otra información. Después de la demostración del plan, el mantenimiento anual se lleva a cabo paso a paso.
Por otro lado, el mantenimiento mecánico anual del equipo requiere que el reparador lidere y el operador ayude. Los operadores plantean necesidades de mantenimiento para cada máquina, y el Departamento de gestión de equipos recibe e integra con los artículos de mantenimiento anuales convencionales, introduciendo planes de mantenimiento, incluyendo el nombre del equipo de mantenimiento, la parte o el contenido del mantenimiento, la fecha prevista, la fecha de finalización, el personal de mantenimiento, el aceptador, el Jefe del equipo confirma, hay problemas y otra información. El proceso de mantenimiento conjunto entre operadores y operadores de equipos es el proceso de intercambiar experiencias de mantenimiento y operación entre sí y profundizar la comprensión de la estructura y el principio de las piezas de equipo. Si el mantenimiento anual es necesario, se invita a los fabricantes de equipos a participar en la orientación para proporcionar mantenimiento y capacitación profundos, lo que puede hacer que el trabajo de mantenimiento sea la guinda del pastel. Después de la finalización del mantenimiento mecánico, el equipo debe reservar tiempo suficiente para la verificación, prueba y micropuesta en marcha, y luego programar la producción para evitar la producción formal sin problemas.
2.4.4 pasos de operación de equipos estandarizados
La estandarización de los procesos operativos, es decir, la formación de un ritmo de trabajo consistente para todo el personal, puede garantizar que el equipo evite daños causados por factores humanos y algunos accidentes de Seguridad. Las instrucciones de operación estándar o los protocolos de operación del equipo juegan un papel rector en ellos. Organizar regularmente a todos los operadores para estudiar y discutir los documentos de orientación de la tarea, reparar los documentos de orientación en el estudio y corregir diversas operaciones en el autoexamen. Para el personal calificado de alto nivel, se alienta a estudiar y discutir en profundidad las instrucciones del equipo de los fabricantes de equipos para ampliar el conocimiento de los principios del equipo. El responsable general del equipo debe establecer una cuenta de préstamo de instrucciones del equipo, y el operador debe completar el estudio y el registro dentro del tiempo prescrito. Además, se llevan a cabo diversas formas de capacitación y evaluación teórica y práctica de los operadores. Evaluar regularmente el nivel de habilidades de los operadores de reanudación y ajustar dinámicamente el nivel de habilidades de los operadores, manteniendo así la vitalidad de todo el equipo y evitando la degradación o el agotamiento de las habilidades de los operadores. La evaluación práctica de los operadores de equipos debe ser evaluada por el responsable del equipo en coordinación con el supervisor de producción y el supervisor del equipo, y los resultados de la evaluación son más objetivos e imparciales.
2.4.5 mejorar el plan de evaluación de los trabajadores de mantenimiento de equipos
Fortalecer el diseño del plan de evaluación de los trabajadores de mantenimiento, explorar gradualmente el mecanismo de evaluación y puntuación de los trabajadores de mantenimiento, a fin de reflejar el nivel de trabajo de mantenimiento de manera justa, objetiva, verdadera y meticulosa. La evaluación de los trabajadores de mantenimiento no puede ser realizada solo por los gerentes de mantenimiento, sino también por el Departamento de producción y los operadores para mejorar el mecanismo de retroalimentación y supervisión del trabajo de mantenimiento. El ciclo de evaluación de los trabajadores de mantenimiento de equipos no debe ser largo, para evitar olvidar que los eventos afectan la precisión de la evaluación. Los operadores deben establecer una cuenta de mesa de trabajo de servicio de mantenimiento para los trabajadores de mantenimiento en su trabajo diario, registrar los asuntos que los trabajadores de mantenimiento deben mejorar para presentarlos en el momento de la evaluación, lo que ayuda a mejorar el nivel de trabajo de mantenimiento de primera línea.
2.4.6 Plataforma de comunicación fluida
Las empresas lácteas tienen muchas líneas de producción, largos tiempos de producción y alta frecuencia de turnos entre operadores, por lo que es muy necesario fortalecer el intercambio de experiencias y la entrega de trabajo. Utilizar Wechat y software empresarial para construir una plataforma de comunicación, alentar el fortalecimiento del intercambio de experiencia laboral y situación de servicio, eliminar las barreras de trabajo y formar una red de supervisión de equipos, una red de mantenimiento y una red de operación que se integren entre sí. Con el aumento de la comunicación, cada vez hay menos problemas de falla en el sitio.
2.4.7 parámetros del dispositivo de respaldo de archivo regular
Establecer un plan de almacenamiento regular de los parámetros del equipo, hacer copias de Seguridad y llamar a tiempo si es necesario. Algunos dispositivos están inactivos durante mucho tiempo, lo que afectará el funcionamiento debido a la pérdida de parámetros de control, y los parámetros se toman fotos y archivan regularmente para hacer copias de seguridad, lo que puede ahorrar tiempo y costos de recalibración o prueba de los parámetros del equipo. Evitar accidentes graves de parada y suspensión de la producción.
3.1 cambios que se producen tras la implementación del TPM
Después de la implementación del sistema tpm, las empresas redujeron costos y aumentaron significativamente la eficiencia, la pérdida de todo tipo de materias primas y materiales de embalaje de equipos relacionados disminuyó constantemente, y la tasa de falla de equipos se redujo considerablemente, eliminando el riesgo de suspensión de fallas y escasez. Ayudar efectivamente a mejorar el nivel de gestión del equipo, aumentar el entusiasmo de todo el personal, responder rápidamente a las fallas y aumentar la conciencia del mantenimiento preventivo. El sentido de responsabilidad y la capacidad de comunicación de los trabajadores de mantenimiento de primera línea se han mejorado y la capacidad práctica se ha fortalecido. Las habilidades de mantenimiento de los operadores se mejoran simultáneamente, y la responsabilidad y la agresividad se fortalecen. El mecanismo de registro y mantenimiento de fallas del TPM está básicamente establecido y funciona sin problemas. Mejorar aún más la eficiencia de la producción de productos y satisfacer las necesidades de la expansión y apertura continua del mercado.
3.2 problemas y contramedidas en la aplicación del TPM
A nivel macro, la penetración del pensamiento TPM en el Departamento de equipos de producción es insuficiente, por lo que es necesario aumentar la publicidad, la edificación y la capacitación del pensamiento tpm. El Jefe general del equipo debe fortalecer la supervisión continua del mantenimiento y mantener el funcionamiento y la mejora del sistema. En caso de conflicto con los arreglos de mantenimiento, es necesario ordenar el nivel de prioridad de mantenimiento del equipo, esforzarse por fortalecer el mantenimiento prioritario del equipo de alto valor de producción, y luego mantener el equipo de bajo valor de producción, para que el mantenimiento se lleve a cabo efectivamente según sea necesario y según lo planeado. En términos de estadísticas de tasa de falla, es necesario distinguir entre la temporada baja y la temporada alta, y puede haber grandes desviaciones entre la temporada baja y la temporada alta. La carga de trabajo de las estadísticas de datos es grande, si se pueden utilizar sistemas inteligentes y sistemas de Big data para realizar estadísticas automáticas, se pueden ahorrar más recursos humanos y materiales.
A nivel microscópico, la desviación del comportamiento de mantenimiento de los operadores requiere una corrección continua, utilizando el sistema de consulta de reproducción de videovigilancia, monitoreando de vez en cuando el comportamiento de mantenimiento diario de primera línea, mejorando constantemente la eficiencia del mantenimiento y estimulando de manera integral el entusiasmo de los operadores.
El TPM se aplica en la gestión de equipos lácteos, y la práctica ha demostrado que las medidas son factibles y efectivas. hoy en día, el TPM se aplica ampliamente en todos los ámbitos de la vida y desempeña constantemente su papel. El TPM desempeña un papel importante en la reducción de la tasa de fallos de los equipos, la mejora de las habilidades de mantenimiento de los equipos de producción y operación, la mejora de la calidad de los productos y la reducción de accidentes. la implementación del funcionamiento del sistema TPM puede ayudar al rápido desarrollo de las empresas.